微弧氧化(Microarc oxidation, MAO)又稱等離子體電解氧化(Plasma electrolytic oxidation, PEO)、微等離子體氧化(Microplasma oxidation, MPO)等,是通過電解液與相應電參數(shù)的組合,在鋁、鎂、鈦等金屬及其合金表面依靠弧光放電產(chǎn)生的瞬時高溫高壓作用,原位生長出以基體金屬氧化物為主的陶瓷膜層。
微弧氧化工藝將工作區(qū)域由普通陽極氧化的法拉第區(qū)域引入到高壓放電區(qū)域,克服了硬質陽極氧化的缺陷,極大地提高了膜層的綜合性能。微弧氧化膜層與基體結合牢固,結構致密,韌性高,具有良好的耐磨、耐腐蝕、耐高溫沖擊和電絕緣等特性。該技術具有操作簡單和膜層功能可控的特點,而且工藝簡便,環(huán)境污染小,是一項全新的綠色環(huán)保型材料表面處理技術,在航空航天、機械、電子、裝飾等領域具有廣闊的應用前景。
如圖1所示,將鋁、鎂、鈦等有色金屬或其合金置于電解液中作為陽極,在微弧氧化專用電源所提供的外加電場作用下,使材料的表面在高于法拉第放電區(qū)外的微弧區(qū)電壓作用下產(chǎn)生微弧放電,微弧放電產(chǎn)生瞬間高溫高壓,在熱化學、等離子體化學和電化學等因素的共同作用下,使得有色金屬材料近表面內(nèi)發(fā)生復雜的電化學反應、等離子體運動、材料相變、溶液離子電泳運動等物理、化學、電化學過程,從而導致材料表層物質發(fā)生電擊穿、熔化、化學反應、凝固、擴散、相變等一系列物理化學變化。在高溫高壓以及這些復雜反應的共同作用下,在基體材料表面便形成了性能優(yōu)異的陶瓷膜層。由于鋁、鎂、鈦氧化物的高阻抗特性,在相同電參數(shù)條件下,較薄的膜層區(qū)域總是優(yōu)先被擊穿放電而生長增厚,這樣最終使得材料表面生長一層均勻致密的陶瓷膜層。同時還可以根據(jù)需要調(diào)整電解液的配方,從而在材料表面生成具有不同性能的陶瓷膜層。該技術的基本原理類似于陽極氧化技術,所不同的是利用等離子體弧光放電增強了在陽極上發(fā)生的化學反應,這也是該種膜層綜合性能優(yōu)于陽極氧化膜層的原因。 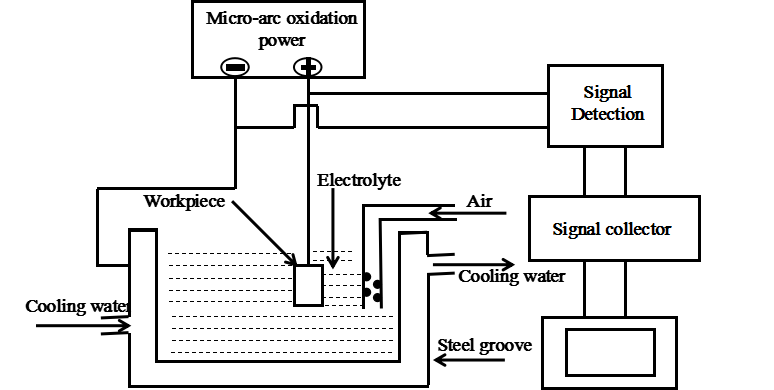
圖1 微弧氧化技術原理示意圖 微弧氧化處理過程 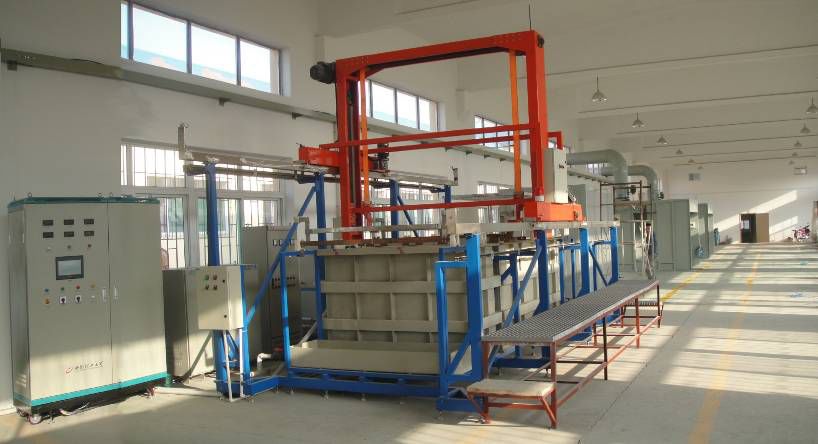
圖2為根據(jù)微弧氧化技術原理設計制造的生產(chǎn)線
微弧氧化處理能力強,可以處理各種形狀復雜的工件,能在試件的內(nèi)外表面生成均勻陶瓷層;對材料的適應性廣,除鋁、鎂、鈦金屬及其合金外,還能在鋯、鉈、鈮等金屬及其合金表面生長陶瓷膜層。 微弧氧化電解液對環(huán)境基本無污染,整個處理過程中無有害廢水和廢氣產(chǎn)生,綠色環(huán)??沙掷m(xù)發(fā)展。 整套設備、工藝簡單,處理工序少,無須經(jīng)過酸洗、堿洗等前處理工序,除油后可直接進行微弧氧化處理,易于實現(xiàn)自動化生產(chǎn)。 處理效率高,一般陽極氧化獲得30μm左右的陶瓷層需要1~2h,而微弧氧化只需10~60min即可。 陶瓷膜層與基體以冶金方式進行結合后原位生長,兩者結合緊密,膜層與基體有較好的結合力,不易剝落。 陶瓷膜層擁有比較好的綜合性能,如具有良好的耐蝕性、耐磨性、高硬度等,此外還能制備出具有隔熱、催化、抑菌、生物親和性等其它特殊功能的膜層。 表1列出了微弧氧化與陽極氧化膜的性能指標對比情況。從中可以看出微弧氧化膜的性能較陽極氧化及硬質陽極氧化膜的各項性能指標有顯著的提高。 圖3為微弧氧化膜層的典型形貌。表面盲孔微區(qū)分布均勻(見圖3a),有利于減摩條件下連續(xù)油膜的形成,改善潤滑條件,降低摩擦因數(shù),延長使用壽命。對用于防腐保護涂層,此類表面狀態(tài)也有利于進行封孔或噴粉等后續(xù)處理,增強其附著力;膜層與基體以冶金型微熔過渡區(qū)連接,其組織致密無穿孔(見圖3b),因此膜層與基體結合牢固。表2為不同微弧氧化膜層的性能指標。 圖3 微弧氧化膜層的典型形貌照片 (a) 表面;(b) 截面 微弧氧化技術廣泛應用于航空、航天、兵器、機械、汽車、電子、交通、石油化工、紡織、印刷、醫(yī)療等行業(yè)鋁、鎂、鈦及其合金的防腐耐磨耐熱絕緣處理。此外,還可用于:噴粉的前處理、噴漆的前處理、電泳的前處理、可替代污染嚴重的電鍍硬鉻及可替代工藝復雜且污染嚴重的陽極氧化等領域。 以下為微弧氧化技術在鋁合金、鎂合金及鈦合金零部件表面處理上的一些應用實例照片。
|